Imagine a world without cars, airplanes, or even simple tools. It’s hard to picture, isn’t it? That’s the reality if we didn’t have the ability to shape metals into the forms we need. This process, known as casting, relies on a fundamental step: the controlled introduction of molten metal into molds. This seemingly simple act is a marvel of engineering, requiring precision and understanding to produce quality castings.

Image: intechvietnam.com
My first encounter with this fascinating process was during a visit to a foundry. Witnessing the molten metal pouring into intricate molds, I was struck by the sheer power and meticulousness involved. The whole process seemed like a delicate dance between heat, pressure, and form. That day, I realized the importance of controlled access for molten metal and how this seemingly simple act is the foundation of an entire industry.
Understanding the Access Mechanisms
The way molten metal is introduced into the mold is crucial for the quality and efficiency of the casting process. A variety of methods have been developed over the years, each with its own advantages and drawbacks. They can be broadly classified into two main categories: gravity-fed and pressure-fed systems.
Gravity-fed systems, the most common and simplest, rely on the force of gravity to pull the molten metal into the mold cavity. Think of a teapot pouring tea into a cup. This method is cost-effective and easy to implement, but it’s less suitable for complex designs requiring precise filling and can result in uneven filling, particularly for large or intricate castings.
Pressure-fed systems, on the other hand, use external pressure to force the molten metal into the mold. This method is ideal for complex shapes and intricate designs, ensuring uniform filling and reducing defects like air pockets.
Unveiling the Science Behind Controlled Access
The success of any casting process hinges on how accurately and efficiently the molten metal is injected into the mold. This seemingly simple step involves a complex interplay of factors, including:
Flow Rate and Pouring Temperature
The rate at which molten metal enters the mold, also known as the flow rate, significantly impacts the filling process. Too slow a flow rate can result in incomplete filling, while too high a rate can lead to defects due to excessive turbulence and air entrapment. Similarly, the pouring temperature plays a crucial role. If the molten metal is too hot, it can cause excessive heat stress on the mold, leading to mold damage or casting defects. Conversely, if the temperature is too low, the metal may solidify prematurely, causing filling problems and reducing the casting’s quality.
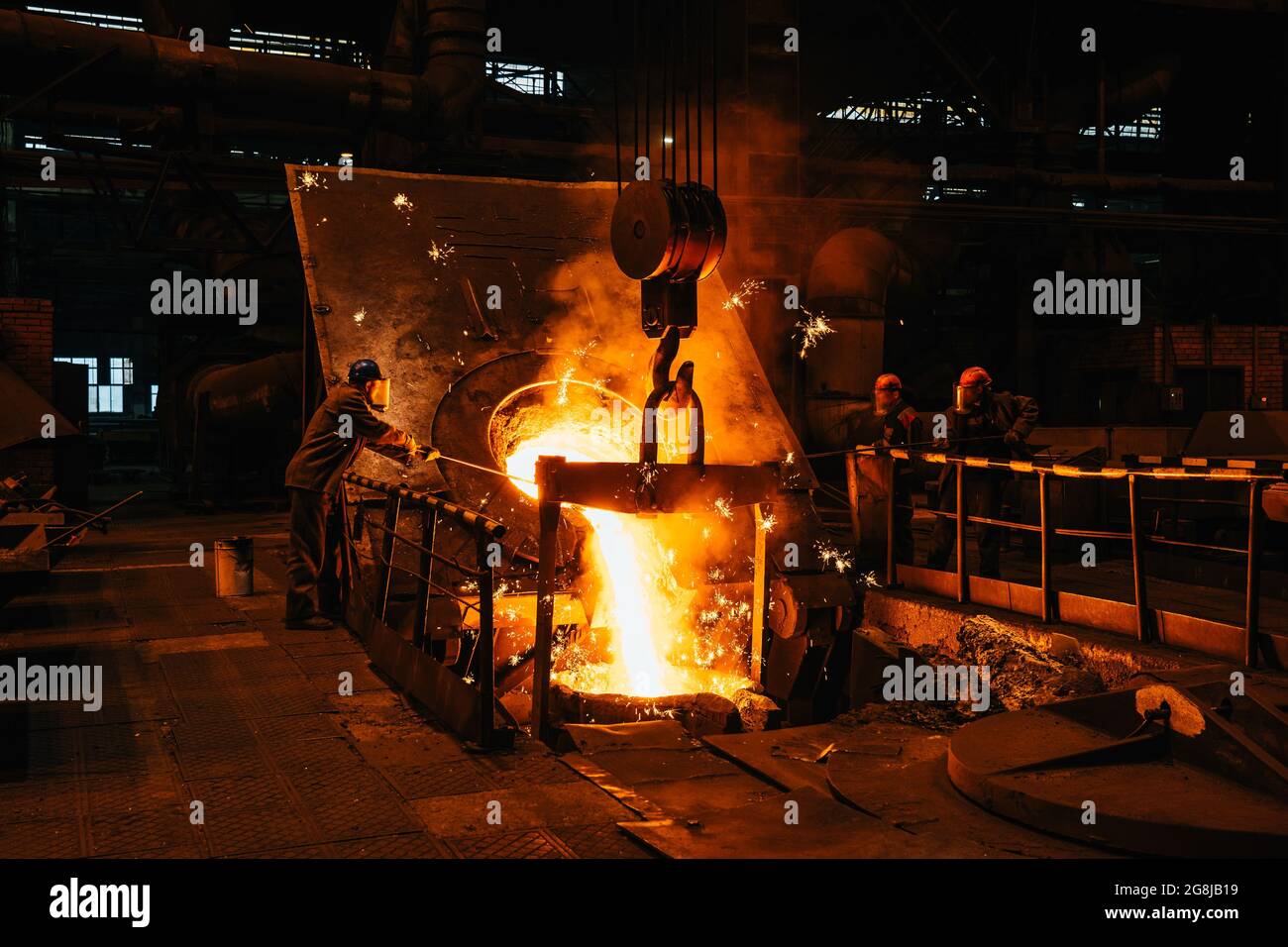
Image: www.alamy.com
Mold Design and Materials
The design of the mold is crucial for creating the desired form in the final casting. It needs to be robust enough to withstand the high temperatures and pressures involved. The materials used for the mold also play a significant part. Traditionally, sand casting molds were used, but more recently, metal and ceramic molds have become popular due to their ability to withstand higher temperatures and produce finer finishes. The material’s ability to conduct heat needs to be considered to avoid premature solidification and ensure proper filling of the mold cavity.
Gate and Runner Systems
The gate, a specifically designed opening in the mold, acts as the entry point for the molten metal. Its shape and size influence the flow rate and pressure within the mold. The gate can be designed to control the flow direction and speed, ensuring that the molten metal fills the mold evenly. The runner system, a network of channels connected to the gate, distributes the molten metal throughout the mold cavity, guaranteeing uniform filling and reducing defects.
Trends and Innovations in Molten Metal Access
The quest for improved efficiency and precision in casting processes continues. Technological advancements are constantly shaping how molten metal is accessed and managed. Here are some key trends:
- Computer-Aided Design (CAD): CAD software has revolutionized mold design, allowing engineers to create intricate and complex molds with greater precision. This enables complex and precise filling of the mold cavity with molten metal, leading to castings with superior accuracy and reduced defects.
- Simulation Software: Simulation software allows engineers to predict how molten metal will flow through the mold under various conditions. This helps optimize the gate and runner systems, minimizing filling problems and ensuring efficient casting production.
- Automated Casting Machines: Automation is transforming the casting industry, increasing efficiency and reducing human error. Automated casting machines offer precise control of pouring temperature, flow rate, and other critical parameters, leading to consistent and high-quality castings.
Expert Tips for Effective Molten Metal Access
Drawing from my experience in the industry, here are some tips for achieving optimal molten metal access and ensuring quality castings:
- Get the pouring temperature right: It’s crucial to use the correct pouring temperature for the specific metal alloy and mold material. Too high a temperature can cause defects and mold damage, while too low a temperature can lead to premature solidification and incomplete filling.
- Optimize the gate and runner system: The design of the gate and runner system is crucial for directing the flow of molten metal and preventing defects. Ensure they are correctly sized and positioned to ensure even filling and minimize turbulence.
- Embrace simulation software: Simulation software can greatly optimize the entire process, minimizing trial and error and saving time and resources. It allows you to see how the molten metal will flow and make necessary adjustments to the mold design and pouring process.
- Invest in quality control measures: Regularly monitor pouring temperature, flow rate, and other parameters to ensure consistency and prevent defects. Implementing good quality control practices can significantly improve the quality and efficiency of your casting operation.
FAQ:
Q: What are some common defects in castings caused by poor molten metal access?
A: Common defects include:
- Incomplete filling: The molten metal doesn’t completely fill the mold cavity.
- Cold shuts: The molten metal solidifies prematurely, creating a gap or void within the casting.
- Air entrapment: Air pockets form within the casting, creating weak spots and potential failure points.
- Misruns: The molten metal flows unevenly, resulting in an incomplete or distorted casting.
Q: What are some common materials used for molds?
A:
- Sand: Widely used, inexpensive, and versatile but can produce rougher finishes.
- Metal: Offers durability and allows for higher pouring temperatures but can be expensive and require specialized equipment.
- Ceramic: High-strength, heat-resistant, and can produce smooth finishes but can be brittle and expensive.
Access For Molten Metal Into Molds
Conclusion
The successful access of molten metal into molds is a critical step in the casting process, ensuring the creation of high-quality castings. By understanding the science behind controlled access, embracing technological advancements, and implementing best practices, you can optimize this process and produce superior castings.
Are you interested in learning more about the captivating world of metal casting and the science of controlled access? This topic is full of intriguing information, and I encourage you to explore further! Let me know if you have any questions or if there are other aspects of the casting process you’d like to learn about.